These Christmas gift bags are so much fun to make though they do take time. I really like the fact they can be used every year.

I first learned out to make these bags at Embroidery Club a couple of years ago. The bag was for a wine bottle and I ended up adapting it to get a gift bag. I don’t do the embroidery any more and won’t unless it is a gift for a special person.
For these bags you will need:
- 2 – 13” squares of printed fabric (Christmas or otherwise)
- 2 – 13” squares of light weight interfacing
- 2 – 4 x 13” rectangles for the cuff of the bag. It can be plain, marbled, or a small print.
- 2 – 4 x 13” rectangles of light weight interfacing
- 2 – 13 x 16.5” rectangles of lining fabric (I use broadcloth)
- 2 – 13 x 16.5” rectangles of light weight interfacing
I cut this bags lining and interfacing only 16” for a small amount of the cuff turned to the inside of the bag. - ribbon
- Optional 2 – 1 x 13” pieces of a contrasting fabric ( will make the bag with them this time)

Iron the interfacing on to all the pieces of the bag. Trim interfacing that shows if necessary.
Fold the 2 pieces of 1 x 13” pieces in half so they are 1/2” x 13”.

Lay the long thin pieces onto the cuffs with raw edges to raw edges. Pin into place and stitch 1/8” from raw edge.

Pin the raw edge of the stitched piece to the top of the bag making sure any print is going in the right direction. Stitch in place using a 1/4” seam. Press seam allowance up to the cuff.

Mark the button hole in the center of one piece. I marked 1” from the seam line and then marked the button hole up 1/4” from that line.

Stitch the button hole starting at the bottom of the top line. My button hole is 13 mm and they can be as long as 15 mm. Snip the button hole open. I apply Fray Block prior to cutting the button hole open. Your choice.

Pin one side together making sure the cuffs and the little trim match nicely. Sew with 1/4” seam allowance. Press the seam open. Repeat with the other side.

Pin the bottom together and sew a 1/4” seam from the stitching line to the stitching line of each side seam. Do not sew the piece of seam allowance that is a single layer.

Press the bottom seam allowance open. Next take the side seam and bottom seam and match them up to make a triangle. Pin through both the seams and smooth out so there are no folds on both sides.

Using a 6” ruler and the 45 degree lines, have the triangle of the fabric match up to the triangle on the ruler.
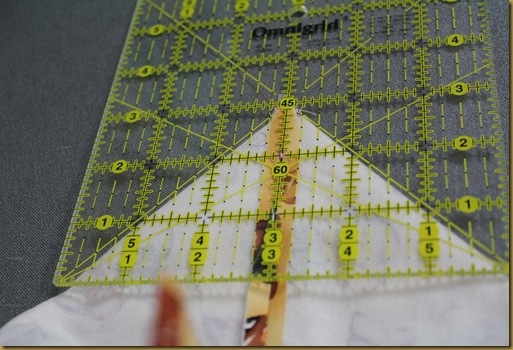
I use a chalk liner to make a stitching line across the the base of the triangle. As you can see I have set the line coming down the seam at 3” but you can do 2” or 2.5” if you wish. Sew across the chalk line. I do both of these at the same time.

Fold and press the stitch line so the triangle flips up the side seam.
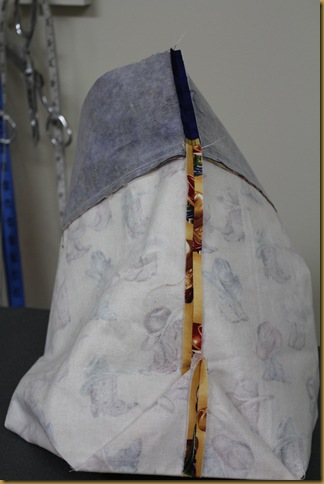
Your outer bag is done. The lining is done the same way except you do not add a cuff at the top and you leave an opening in one of the side seams. That is where you will turn your bag to the right side.

Both the lining and outer bags are done. Have the lining turned inside out.

Take the outer bag and put into the lining. Match up the side seams and pin around the top. Stitch the tops of the two bags together with a 1/4” seam.

Pull the outer bag through the opening in the lining so both bags are now right side out.

I press the joining seam towards the outer bag. Push the lining into the outer bag and arrange to fit. Mine had a bit of the cuff on the inside (just trying something new).

I used a quilting marker on my sewing machine and stitched 1” down on the print of the outer bag. I then used my ditch foot to sew in the ditch where the print meets the cuff. This makes a casing for the ribbon.
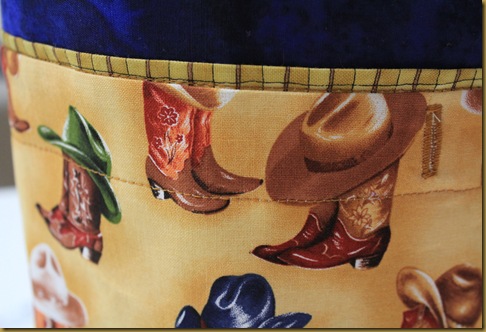
At the top of the cuff, I top stitched 1/4” down. I ladder stitch the opening in the lining to close it up neatly. Then I threaded a ribbon through the button hole to tie the bag shut.
